Abstract
In this case study, we explore how a global leader in the printing industry revolutionized equipment maintenance through digital transformation. By shifting from a reactive to a predictive maintenance model, the company implemented an automated Maintenance Management System that streamlined service processes, reduced downtime, and optimized operational costs. This transformation enabled maintenance managers to efficiently track equipment status, assign work orders, and provide technicians with digital instructions, eliminating manual inefficiencies. The case study highlights the impact of predictive maintenance in enhancing service reliability and operational efficiency.
About Our Client
A global leader in the printing industry transformed their customers’ printing equipment CapEx problem to an OpEx one, by offering ‘Print as a Service’ solution. This business innovation helped the end customer to focus on their core business instead of printing issues.
Business Challenges
Proactive Maintenance Strategy:
A shift from a reactive to a proactive maintenance approach for large printing equipment, ensuring timely service and reducing reliance on customer complaints.
Cost-Effective Predictive Maintenance:
Leveraging predictive maintenance to minimize the total cost of ownership and maintenance of the printing equipment.
Paper based manual process:
Maintenance and service schedules were paper-based for a huge network of equipment.Incomplete data capture of the service activities leading to low level analytics.
Digitization with huge manuals:
Digital transformation had to integrate with physical equipment service tools, parts, and volumes of task instruction manuals.
Solution Details
- True digital transformation – The Maintenance Manager 4.0 was developed as an automated solution for tracking and monitoring equipment maintenance.
- A web interface was designed that contained the database of all the equipment with their respective maintenance priorities. The maintenance managers could create work orders based on the maintenance urgency of the equipment and assign them to technicians. All maintenance instructions were made available digitally.
- Smarter Maintenance – A mobile interface notified the technicians of their work orders that provided detailed maintenance instructions. It also allowed them to update task completion, and other relevant data. The service instructions specific to the equipment parts were available in the mobile interface, doing away with the time-consuming search for instructions from heavy manuals.
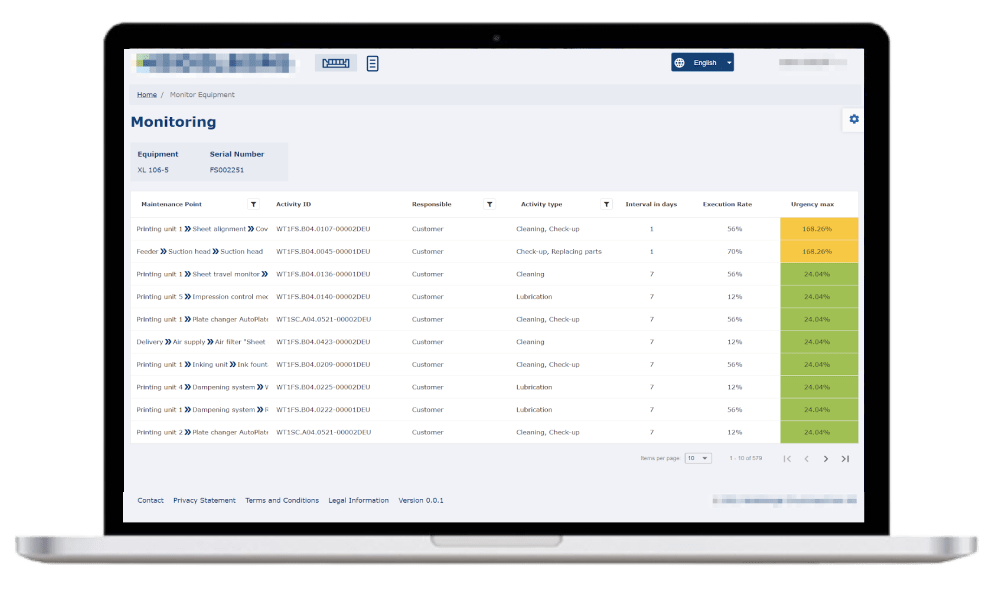
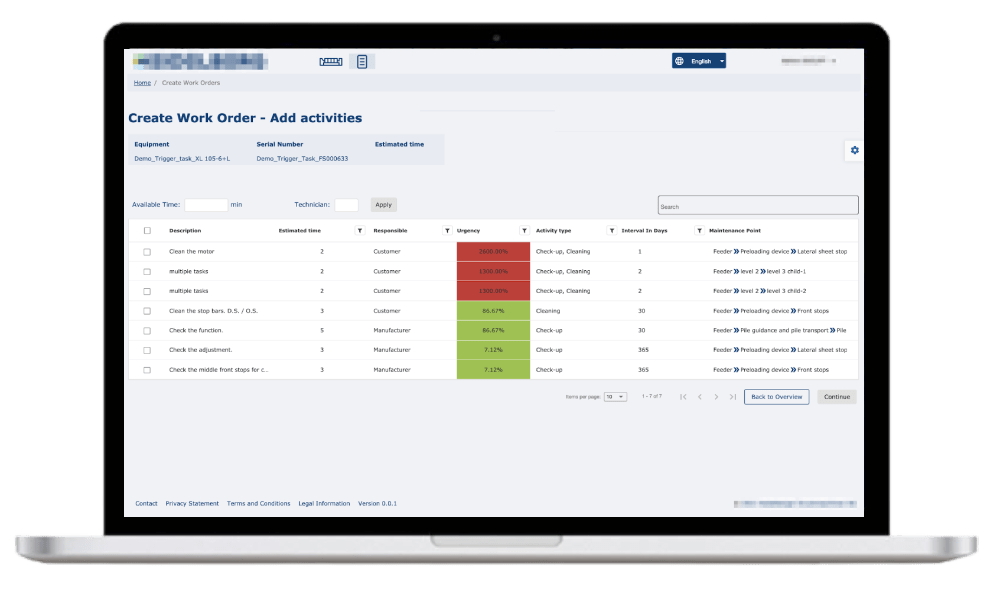
Integrating all activities related to equipment maintenance.
Minimizing equipment downtime with systematic preventive maintenance schedules.
Technicians have clear instructions, and necessary parts are readily available digitally, saving time and improving ROI.
Providing real-time insights into maintenance efforts.
Ensuring complete data on the condition and performance of equipment.
Comprehensive maintenance data, including images, helps predict equipment lifespan and supports end-of-life planning.